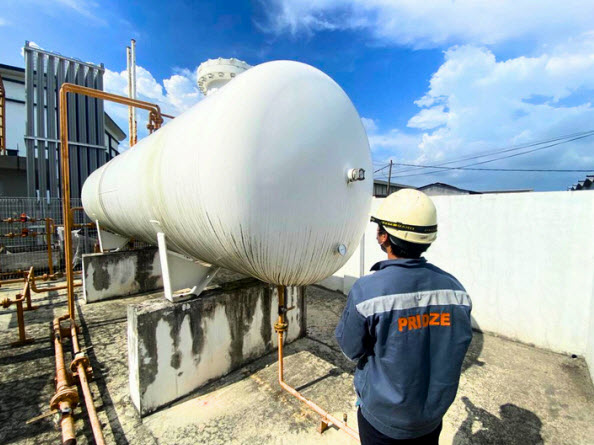
Engineering
Engineering, Procurement, Construction, and Commissioning (EPCC) in LPG Projects
1. Engineering (E)
The engineering phase for LPG projects involves detailed design and planning to ensure the safe and efficient handling, storage, and distribution of LPG. It includes:
- System Design and Layout:
- Designing the entire LPG storage, distribution, and handling system, including storage tanks, bottle filling stations, distribution pipelines, safety systems (e.g., pressure relief valves), metering systems, and control systems.
- Planning the LPG pipeline network, considering factors like flow rates, pressure, distance, and environmental considerations.
- Safety and Risk Analysis: Conducting HAZOP (Hazard and Operability Studies) and FMEA (Failure Modes and Effects Analysis) to evaluate potential risks and ensure that safety mechanisms like gas leak detection, emergency shut-off valves, and ventilation systems are integrated into the design.
- Environmental Considerations: Ensuring compliance with environmental regulations by incorporating mitigation measures for gas leaks, fire hazards, and emissions.
- Automation and Control Systems: Developing control systems that regulate the flow of LPG, pressure, and temperature in storage tanks, and integration of Supervisory Control and Data Acquisition (SCADA) systems for remote monitoring.
2. Procurement (P)
The procurement phase involves sourcing and acquiring all the necessary equipment, materials, and services for the LPG project. This is a critical phase because the reliability and safety of the entire LPG system depend on the quality and performance of the procured items.
- Equipment and Materials Sourcing:
- Procuring LPG storage tanks, pressure vessels, pipes, valves, meters, regulators, fire suppression systems, and other critical components.
- Choosing suppliers and manufacturers that meet ISO standards (e.g., ISO 9001 for quality management) to ensure the equipment is reliable, compliant with safety codes, and suitable for the specific LPG application.
- Vendor Selection and Management: Engaging with reputable vendors who can provide high-quality materials on time. Procurement teams negotiate contracts, manage logistics, and ensure that the procurement process aligns with the project’s schedule and budget.
- Logistics and Delivery: Coordinating the delivery of materials and equipment to the project site, considering customs and international shipping (if importing), and ensuring that components arrive in good condition and on time.
3. Construction (C)
The construction phase encompasses the physical building of the LPG infrastructure, including storage tanks, pipelines, bottling plants, distribution systems, and other associated facilities. This phase requires stringent attention to safety, quality control, and schedule management.
- Site Preparation:
- Clearing and preparing the site for installation, which may include excavation, leveling, and constructing necessary access roads or facilities.
- Tank and Pipeline Installation:
- Installation of LPG storage tanks (above-ground or underground), ensuring that safety features like pressure relief valves, venting systems, and grounding are properly incorporated.
- Constructing distribution pipelines, valve stations, regulators, and associated equipment while ensuring compliance with local and international piping codes (e.g. MS830, MS930, ASME, API standards).
- Fire and Safety Systems:
- Installing fire suppression systems (e.g., foam, CO2 systems) and leak detection sensors to minimize the risk of explosions or fires.
- Implementing ventilation systems for proper gas dispersion in case of leaks, when necessary.
- Quality Control: During construction, teams perform regular inspections to verify that the installation meets safety and engineering standards. Non-destructive testing (NDT) methods such as radiography or ultrasonic testing may be used to check for faults in welding and materials.
4. Commissioning (C)
The commissioning phase involves the testing, validation, and integration of all systems to ensure they perform according to design specifications. This phase is critical to ensure that the LPG systems are operationally safe and efficient before handover to the client.
- System Testing and Calibration:
- Testing of storage tanks for integrity, including pressure testing and leak detection.
- Commissioning of LPG pipelines, valves, and meters to ensure proper flow and pressure regulation.
- Testing fire suppression systems, safety devices, and emergency shutdown mechanisms to ensure they work under real operational conditions.
- System Integration and Monitoring:
- Integrating automation and real-time monitoring of LPG flow, pressure, temperature, and storage levels.
- Ensuring proper functionality of alarms and safety triggers to alert operators of abnormal conditions (e.g., gas leaks, pressure surges).
- Operational Training: Training users and relavant personnel on system operation and emergency response procedures.
- Documentation and Handover: Preparing as-built documentation and manuals, and handing over the system to the client after final acceptance testing.
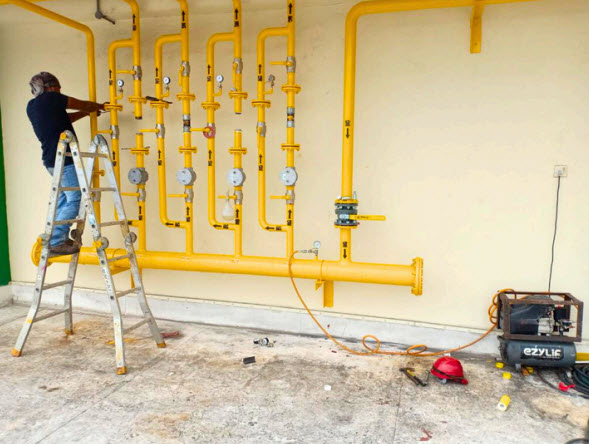
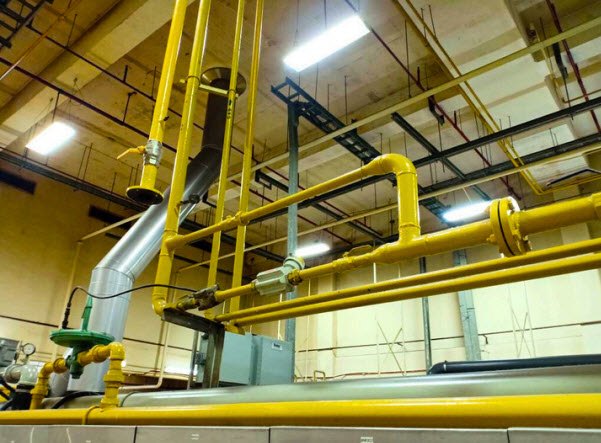
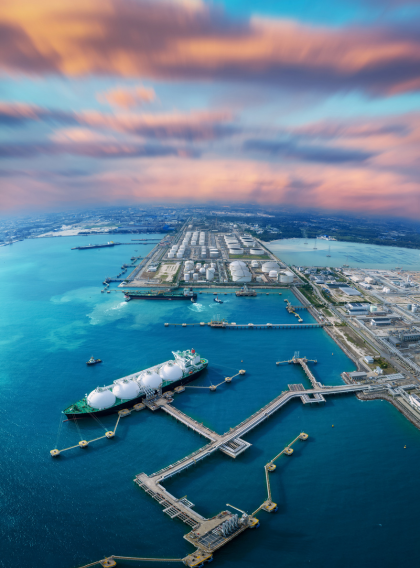