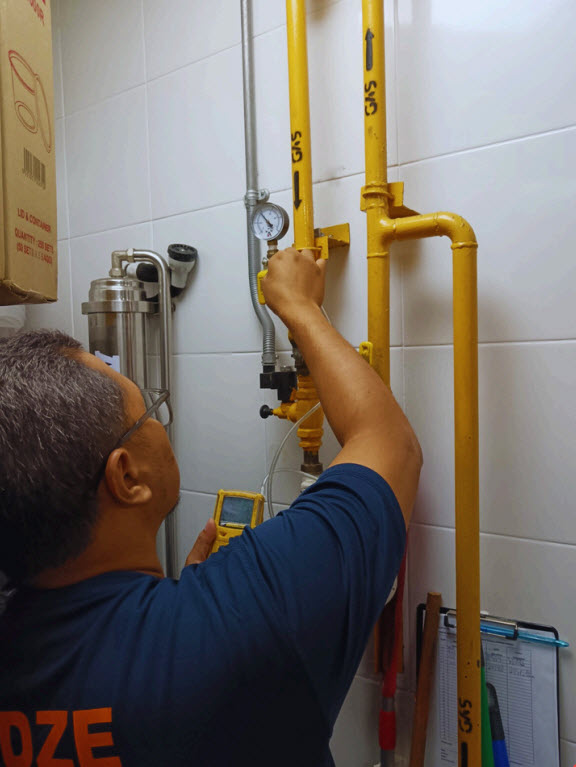
LPG Inspection
Our seasoned professionals carry out inspections on all our clients LPG Cylinder Manifolds
Why LPG Inspections Are Essential
LPG, which is commonly used for heating, cooking, and industrial purposes, poses significant safety risks if not managed properly. Regular inspections are designed to:
- Identify potential hazards (such as leaks, corrosion, or improper connections) that could lead to catastrophic incidents.
- Ensure compliance with local and international safety regulations.
- Maintain the integrity of the LPG system, reducing downtime and the need for expensive repairs.
- Extend the lifespan of LPG equipment by identifying and resolving issues before they become critical.
Components of LPG Systems Typically Inspected
An LPG system includes various components that must be regularly checked to ensure safety and functionality. These components include:
1. LPG Cylinders
- Cylinder Condition: Inspecting the physical condition of the cylinders for any signs of damage, dents, rust, or corrosion, which could lead to leaks or cylinder failure.
- Valve Integrity: Checking the valve and connection points for leaks, signs of wear, or malfunctions. Valves should open and close smoothly without leakage.
- Pressure Relief Valve: Ensuring the pressure relief valve is operational to prevent over-pressurization and potential rupture of the cylinder.
2. LPG Tank Installations (for bulk storage)
- Tank Condition: For bulk LPG tanks, inspection are carried out for external damage, rust, and corrosion. Any structural issues can compromise the tank’s safety and lead to leaks.
- Pressure Testing: Performing hydrostatic pressure tests or other diagnostic tests to ensure that the tank can safely handle the expected gas pressure.
- Tank Supports and Mounting: Verifying that the tank is properly secured, with correct foundations, supports, and anchoring in place to avoid accidents due to shifting or instability.
3. Piping and Distribution Systems
- Pipe Integrity: Inspecting all LPG pipes (whether above or underground) for signs of wear, corrosion, or cracks that could lead to leaks.
- Joints and Fittings: Checking for secure, leak-free connections at joints, elbows, and other fittings. Loose connections can result in hazardous gas leaks.
- Piping Layout: Ensuring the piping is correctly laid out according to safety standards, avoiding places like near electrical installations or areas with excessive heat or mechanical stress.
4. Valves and Regulators
- Valve Functionality: Ensuring that all shut-off and control valves are functioning properly. These valves should open and close easily and seal completely when closed.
- Pressure Regulators: Checking that the pressure regulators are correctly set to ensure the gas is delivered at the correct pressure to prevent over-pressurization or insufficient flow. The pressure regulator’s safety features should be in working order.
- Changeover Valves: If the LPG system uses automatic or manual changeover valves to switch between cylinders, these valves need to be tested to ensure they are functioning smoothly without leaks or interruptions in gas supply.
LPG Manifold Systems
For clients with larger-scale LPG installations (such as in industries, commercial kitchens, or hospitals), manifold systems connect multiple LPG cylinders or tanks to a single system. Inspecting these systems ensures that the cylinders are connected safely, and the distribution of gas is managed properly.
- Valve Operation: Ensuring that the manifold valves operate correctly and that they can safely distribute gas without leakage.
- Leak Checks: The manifold, pipes, and associated connections should be leak-tested to detect any weak points where gas could escape.
- Safety Features: Ensuring that emergency shut-off systems and pressure relief devices are functioning properly.
Gas Appliances and Equipment
- Appliance Connections: Checking all connections between the gas supply and appliances (like stoves, heaters, boilers, or industrial equipment) to ensure that no gas is leaking from the appliance or its connections.
- Flame Checks: Inspecting burners and other equipment to ensure they operate with a stable flame and that no gas is escaping when the appliance is off.
- Ventilation: Verifying that there is adequate ventilation to prevent the accumulation of dangerous gases like carbon monoxide (in poorly ventilated spaces).
Inspection Procedures
The LPG inspection process is typically structured into several steps to ensure thorough coverage and compliance with safety standards. Here is a general procedure followed by most LPG inspection :
1. Visual Inspection
A visual check of all components of the LPG system is the first step. This includes cylinders, tanks, piping, valves, and appliances. Inspection involves looking for obvious signs of damage, corrosion, leaks, or other visible issues.
2. Leak Testing
Leak testing is performed using a gas leak detector, soapy water, or a combustible gas indicator. Any suspected leaks around cylinder valves, pipe joints, connections, or appliance fittings should be reported for immediate action.
3. Pressure Testing
In some cases, especially for larger systems, pressure testing is performed to ensure that the system can safely handle the required operating pressure. This test ensures there are no leaks or weaknesses in the system that could lead to dangerous failures.
4. Regulator and Valve Checks
Pressure regulators, shut-off valves, and emergency shut-off systems are tested to ensure they are working as intended. This might involve turning the gas supply on and off, adjusting pressure settings, or activating fail-safes.
5. Documentation Review
Verification is done to ensure that the installation meets local safety standards and codes, as well as, proper documentation such as installation certifications, maintenance records, and service logs.
6. Functional Test (when neccessary)
After inspecting the equipment and connections, a functional test is conducted to check how well the system works under normal operating conditions. This may involve checking gas flow, burner flame stability, and appliance functionality.
Benefits of Regular LPG Inspections
- Enhanced Safety: Regular inspections identify issues before they cause accidents or malfunctions, significantly reducing the risk of fires, explosions, or asphyxiation from leaks.
- Compliance with Laws and Insurance Requirements: Many insurance policies and local regulations require proof of regular inspections for LPG systems. Non-compliance can lead to penalties or voided insurance coverage.
- System Reliability: Well-maintained LPG systems are less likely to experience unexpected failures, reducing downtime and repair costs.
- Cost Savings: Identifying and repairing minor issues early prevents expensive repairs or replacement of components down the line.
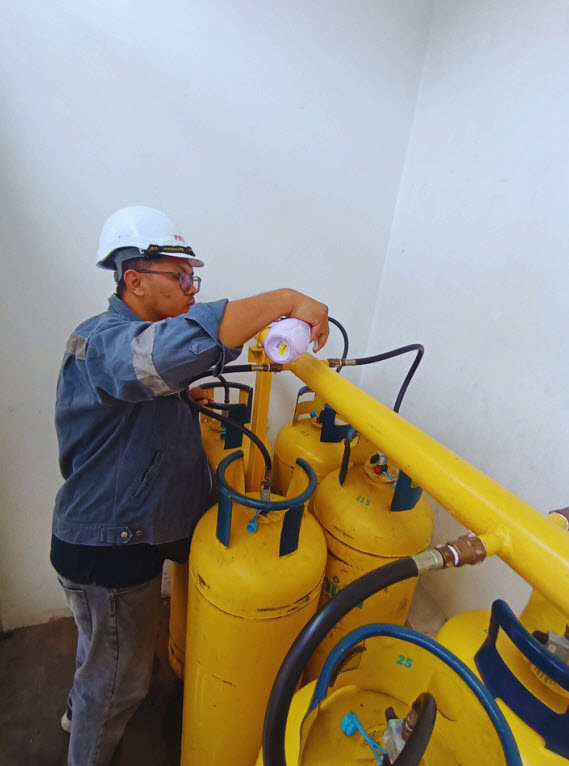
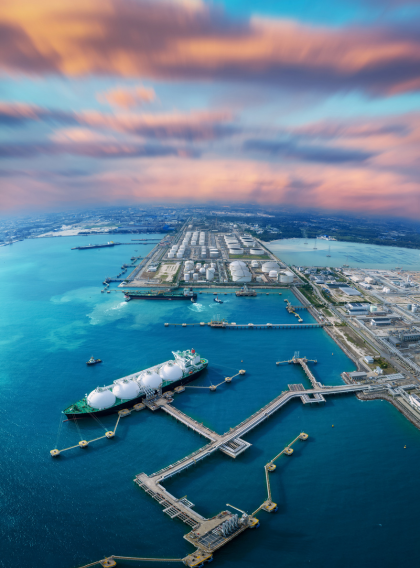